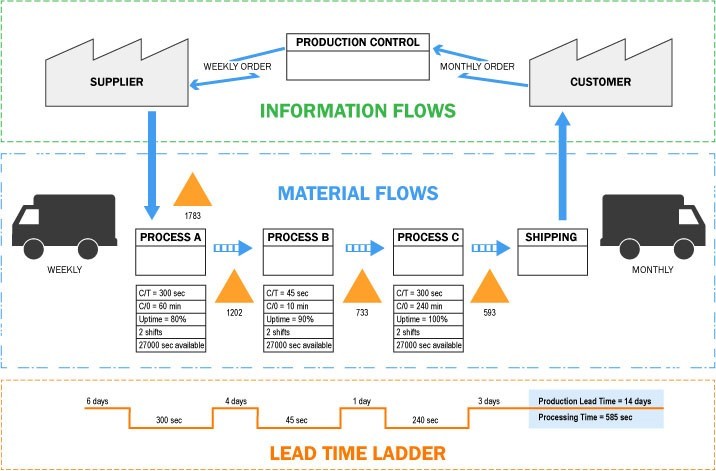
Value Stream Mapping shows where you can improve your process by visualizing both its value-adding and non-value-adding steps.
What Is VSM?
Value stream mapping is a lean manufacturing or lean enterprise technique used to document, analyze and improve the flow of information or materials required to produce a product or service for a customer.
A value stream map displays all the important steps of the work process necessary to deliver value from start to finish. It allows visualizing every task that the team works on and provides single glance status reports about each assignment’s progress. It enables the team and leadership to see where the actual value is being added in the process, allowing them to improve on the overall efficiency associated with the delivery of a product.
VSM can be used for individual products and services for every type of business.
Terminologies in VSM
· Information Flow
This section shows the communication of process-related information and the transmission of data.
· Product Flow
This section maps the steps of the development lifecycle from concept to delivery. It shows both the task being performed & the person or team performing task.
· Cycle time (C/T)
It is the frequency of units produced or the average time between the completed production of one unit to the completed production of the next.
· Setup Time (S/T)
It is the amount of time needed to prepare for a given step.
· Uptime (%)
It gives an idea of the percentage of the total time that the processes or systems are actually active.
· Time Ladder
The Time Ladder provides a visual representation of the value stream timeline.
The upper portion of the time ladder represents the average amount of time that a product spends in the queue or waiting at each stage.
The lower portion of the time ladder shows the average amount of time that each product was actively being worked on, or more specifically when value is actually being added to the product during that specific stage.
How to map the first Value Stream
Define your focus –
This is probably the most important step of the entire VSM exercise. Start with clearly defining the objective. With a clear objective in mind, identify the appropriate focus, scope, and process to be mapped.
Next, determine your fence posts, or the start and endpoints of your mapping exercise. A value stream map is not a process flowchart. It doesn’t need to map every possible inflow or outflow of the process. By maintaining focus on the predetermined objectives and fenceposts, the mapping activity is likely to stay on track and focused.
Go to Gemba (Walk the Process) –
“Go to Gemba” means go to the place where the work is being done. Visit the customer where the production is taking place and understand why they need the features they are requesting.
Define the basic Value Stream –
Start with preparing basic VSM as a starting point. The key thing here is to outline only the process basics and hereafter add the other details step by step.
Develop Current State Value Stream Map –
Starting with the basic VSM add the additional processes and their corresponding data, including current cycle times, lead times, up times, takt times, SLA’s, etc. This should reflect all stages within the defined fence posts, and their respective values as they currently are. This is known as your “Current State” VSM. This current state will be immensely important to keep the process baseline.
From this current state, the mapping team will be able to better understand the entire process. This enables the team to discuss productive what-if and to develop better solutions to identified hot points. It enables to provide a before and after comparison of the process and its performance figures to know if the changes have any desired impact.
Develop Target State Value Stream Map –
Once the current state VSM has been completed, the team will need to develop a Target State VSM. The target state represents a clear target of where you want to end up. These targets can be expressed in delivery velocity, quality-focused metrics, compliance, or any combination of these. The important thing here is to identify a goal to work.
Develop Future State Value Stream Map –
As improvements to the process are identified and planned, the VSM team will need to develop an implementation plan. These improvements will often require a phased approach to introduce necessary changes to achieve the target state.
To do this, a future state VSM should be created for each state of the implementation plan, which typically includes a 30, 60, 90-day view. This allows validating your assumptions at each stage of the implementation plan, to make sure the changes are having the desired impact and moving the value stream performance in the right direction. The future state VSM gives team members a unified view of the overall process as well as targeted objectives to work toward.