A lean organization achieves its goals through the application of time-tested techniques and tools, backed by a firm philosophical foundation of continuous improvement and learning. Behind the lean paradigm are a set of management principles that when consistently applied, result in business success regardless of one’s industry.
What is Lean Management?
Traditionally, we expect management to be the function that is involved in the planning, organizing, directing and controlling resources to achieve organizational goals. In lean thinking, management is the systematic approach of enabling the organization to make its lean initiatives in a focused and efficient manner.
Most organizations fail to sustain their lean efforts due to lack of proper direction from management. The traditional approach of “control” does not work in a lean environment because it does not lend itself to the philosophy of empowering workers to find solutions to the business problems through observation, experimentation, and learning.
The old way of doing things sees managers as people who should provide all the answers to workers on the ground. In lean thinking, however, everybody works together with a clear focus on customer value and continuous improvement.
Lean Thinking Management Principles
The following 14 lean management principles which originated from Toyota provide the philosophical foundation required to achieve success in a lean system. Each has a set of tools that can be used to attain the organizational goals.
These tools are meant to assist a company in achieving results and should not replace a common sense approach to problem-solving. The application of lean tools must happen with the underlying principle in mind. In short, the theory drives the tool and not the other way round.
1. Long-term thinking
The most important factors for success are patience, a focus on long-term rather than short-term results, reinvestment in people, product, and plant, and an unforgiving commitment to quality.
—Robert B. McCurry, former Executive VP, Toyota Motor Sales
Lean thinking organizations have a clear vision of where they want to be in the future. They have a clear picture of what needs to be done to achieve these goals and do not get distracted by the expediencies of the moment. The first principle of lean management is: “Make decisions based on your long-term vision even if means making sacrifices in the short-term.”
The lean tools that drive this principle are:
Hoshin Kanri is a strategic planning tool that ensures the whole organization is aligned to a common goal and leaves little room for diversion. Everybody knows where the company’s direction and their responsibilities in achieving these goals.
Nemawashi is a consensus-based decision-making approach that reduces the time taken to achieve results. By the time a formal meeting is held to make a decision, all involved parties have been consulted and have made up their minds on where they stand on an issue.
2. Flow the Customer Value
This principle deals with identifying wasteful activities that do not add any value to the customer. After determining the wasteful activities, have efforts are made to either eliminate or reduce them. You then align all the other steps in a continuous flow which increases productivity, quality, safety, and morale. There is also a marked reduction in costs as it requires fewer resources for achieving the same results.
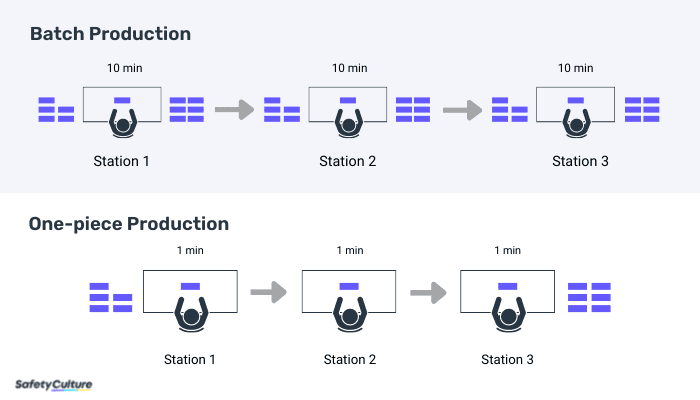
If some problem occurs in one-piece flow manufacturing then the whole production line stops. In this sense it is a very bad system of manufacturing. But when production stops everyone is forced to solve the problem immediately. So team members have to think, and through thinking team members grow and become better team members and people.
—Teruyuki Minoura, former President, Toyota Motor Manufacturing, North America
The lean thinking tools that support this principle are:
Jidoka means building in quality into machines or process to prevent mistakes that have an impact on quality. This tool aims at capturing and correcting errors before they affect the next operation.
Line balancing is used to ensure that equal amount of work passes through the process to avoid the bottlenecks that hinder smooth flow of value
Cellular manufacturing increases flow by consolidating all the prerequisite steps that are required to assemble a product in one place. It also reduces the amount of time used when sub-assemblies move from one station to another
3. Produce at the rate of customer demand
“The more inventory a company has, the less likely they will have what they need” – Taiichi Ohno (Father of the Toyota Production System)
Overproduction means “producing faster or more than the customer is demanding.” It is one of the most costly forms of waste as it encompasses all the known wasteful activities in lean manufacturing. By producing at a rate as close as possible to the real customer demand, costs reduce as there is very little unsalable inventory in place.
The tools that support this principle are:
Kanban system is a signalling device that informs a process what to do next whether it is producing a new product or replenishing raw materials.
Takt time is a metric that determines the rate at which the end customer is demanding a product. All the processes must be synchronized with this rate to avoid non-delivery or over-production
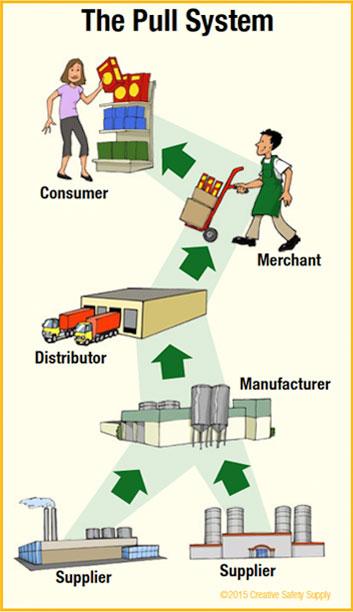
4.Level the workload
In general, when you try to apply the TPS, the first thing you have to do is to even out or level the production. And that is the responsibility primarily of production control or production management people. Levelling the production schedule may require some front-loading of shipments or postponing of shipments and you may have to ask some customers to wait for a short period of time.
—Fujio Cho, President, Toyota Motor Corporation
As companies cannot always produce at the exact frequency of customer demand, production must be evened out across production facilities to ensure prompt delivery. The system works by accumulating a good number of customer orders and then scheduling them at even intervals. Levelling reduces the waste and strain of trying to build to an erratic order. The lean tool used to level the workload is:
Heijunka is the balancing of production to mitigate against the unpredictable spikes in demand that occur in a typical organization. Heijunka stabilizes the production process and ensures the optimal utilization of available resources
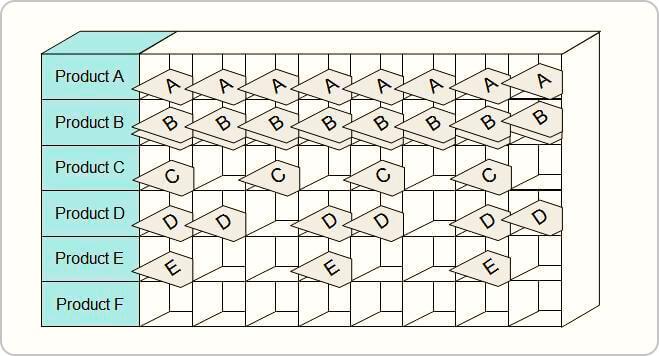
Heijunka Box
5.Quality right the first time
Mr. Ohno used to say that no problem discovered when stopping the line should wait longer than tomorrow morning to be fixed. Because when making a car every minute we know we will have the same problem again tomorrow.
—Fujio Cho, President, Toyota Motor Corporation
A fundamental tenet of lean thinking is that all methods must produce quality parts so that the end product to the customer is defect-free. This principle states that no process should produce, accept or pass on a defective part to the next step. Inspection is a wasteful process because resources have already gone into the production of faulty parts. The aim should be to capture defects before they occur.
The Jidoka tool is also applied here as a means of capturing and reporting the occurrence of a defect. Another closely related device is the andon which is also a signal to the process that an error has occurred that needs correcting.
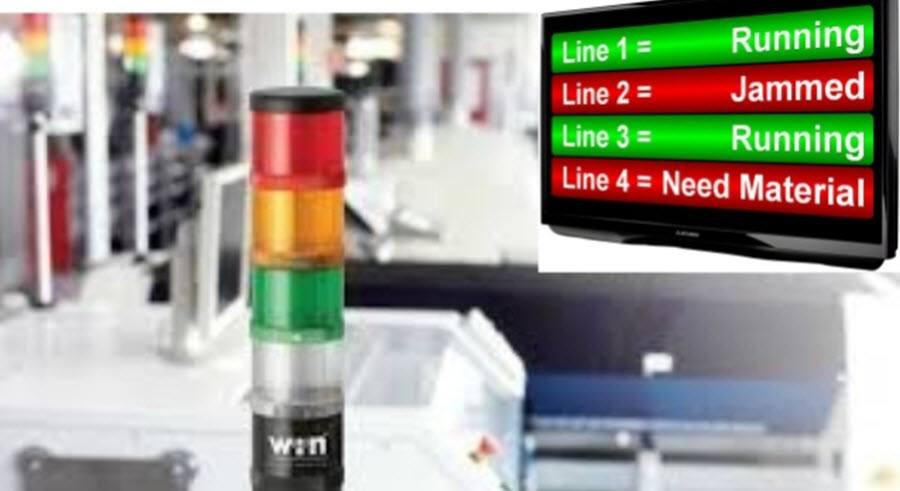
Andon System
6. Standardize and Improve
Standard work sheets and the information contained in them are important elements of the Toyota Production System. For a production person to be able to write a standard work sheet that other workers can understand, he or she must be convinced of its importance…. High production efficiency has been maintained by preventing the recurrence of defective products, operational mistakes, and accidents, and by incorporating workers’ ideas. All of this is possible because of the inconspicuous standard work sheet».
Taiichi Ohno
A standard is the best-known way of doing work. The principle of standardization serves as a reference point for further improvement and also as a means of training new workers on how to complete tasks. Without standards, there can be no way of improving in a lean system.
Improvement on the current way of doing things is a continuous process, and once improvement happens, a new standard must result. Rules are not cast in stone and will change through constant improvement. The tool used to support this lean principle is the Kaizen event.
7. Use visual controls
Mr. Ohno was passionate about TPS. He said you must clean up everything so you can see problems. He would complain if he could not look and see and tell if there is a problem.»
Fujio Cho,
Toyota Motor Corporation, 1999-2005
The purpose of visuals in a lean thinking organization is to communicate in a clear and unambiguous manner to the people working in a process as to the state of that process. Visual control is a lean tool used to bring problems to the surface and afford the workforce an opportunity to solve them.
When problems are hidden, there is no chance of solving them, and this leads to stagnation of the lean initiative. With visual controls, deviations from the acceptable standard are visible and countermeasure to bring the system back online can quickly be taken.
Tools used for visual control include:
5S is a systematic program that helps in orderliness and removal of waste
Process control boards show the status of processes and whether or not they are within specified limits
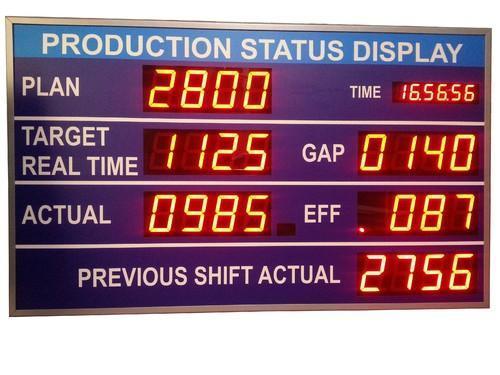
8. Use the right technology
Society has reached the point where one can push a button and be immediately deluged with technical and managerial information. This is all very convenient, of course, but if one is not careful there is a danger of losing the ability to think. We must remember that in the end it is the individual human being who must solve the problems».
Eiji Toyoda,
Challenge and Courage, Toyota Motor Corporation, 1983
Lean thinking organizations do not install technology just because it is the in-thing at the moment. They seriously consider whether the technology will assist them to achieve the goals or whether it will be an impediment to the attainment of value for the customer.
A good example is ERP & MRP systems. While many organizations will rush to install these complex systems, lean thinking firms will first concentrate on the simple problem solving and waste removal tools they have at their disposal. If technology is deemed to be appropriate and relevant to their current issues, the lean thinking firms will surely go ahead and purchase them.
9. Leaders are grown, not bought
Until senior management gets their egos out of the way and goes to the whole team and leads them all together … senior management will continue to miss out on the brain power and extraordinary capabilities of all their employees. At Toyota, we simply place the highest value on our team members and do the best we can to listen to them and incorporate their ideas into our planning process».
Alex Warren, former Senior VP,
former Senior VP, Toyota Motor Manufacturing, Kentucky
This lean management thinking philosophy calls for the development of competent leaders from within an organization rather than always hiring from outside. When this happens, the continuity of business is guaranteed because there is a constant pool of possible leaders who are ready to take over when the time comes.
This constant mentoring of leaders who thoroughly understand the work and live the philosophy of a company is critical in sustaining lean improvements because of maintaining institutional memory.
10. Personal development of people
Respect for people and constant challenging to do better—are these contradictory? Respect for people means respect for the mind and capability. You do not expect them to waste their time. You respect the capability of the people. Americans think teamwork is about you liking me and I liking you. Mutual respect and trust means I trust and respect that you will do your job so that we are successful as a company. It does not mean we just love each other».
Sam Heltman,
Senior Vice President of Administration Toyota Motor Manufacturing, North America (one of the first five Americans hired by Toyota)
Lean continually challenges team members to do their best to solve common business problems. By empowering the workforce to take charge of solving their problems, lean companies improve their skills which ultimately has a significant impact on the business.
The Job Instruction Method perfected at Toyota is one of the essential tools for improving the skills of the workforce in a lean environment.
11. Treat partners with respect
“Toyota is more hands-on and more driven to improving their own systems and then showing how that improves you…”
Toyota is more hands-on and more driven to improving their own systems and then showing how that improves you… Toyota will do things like level their production systems to make it easier on you. Toyota picks up our product 12 times per day. They helped move presses, moved where we get the water from, trained our employees. On the commercial side they are very hands-on also—they come in and measure and work to get cost out of the system. There is more opportunity to make profit at Toyota.
“We started with Toyota when we opened a Canadian plant with one component and, as performance improved, we were rewarded, so now we have almost the entire cockpit. Relative to all lean companies we deal with, Toyota is the best.”
An automotive supplier
Treat suppliers and all other players in the extended enterprise with respect. This principle encourages cooperation and coordination within the extended enterprise which includes suppliers at all tiers. Suppliers and their suppliers are an essential part of the value chain that delivers the needs of the customer.
Lean thinking organizations work with their suppliers and help them to improve for the benefit of all the stakeholders. They understand that their success is dependent on the success of all in a win-win relationship that is defined by mutual respect and cooperation.
12. Gain a first-hand understanding of problems
«Observe the production floor without preconceptions and with a blank mind. Repeat “why” five times to every matter».
Taiichi Ohno,
(as quoted in The Toyota Way document)
This principal focuses on problem-solving that gets to the underlying causes by intimately interrogating the problem at source. The person trying to solve a problem must go to where the problem is occurring and observe the complex interactions of all the parameters before suggesting solutions.
Genchi genbutsu means “go and see” the source of a problem and find out what the exact causes are. It is a lean way of thinking that is not satisfied with second-hand reports but calls for real confirmation at the ground.
13. Build consensus before acting
«If you’ve got a project that is supposed to be fully implemented in a year, it seems to me that the typical American company will spend about three months on planning, then they’ll begin to implement. But they’ll encounter all sorts of problems after implementation, and they’ll spend the rest of the year correcting them. However, given the same year-long project, Toyota will spend nine to 10 months planning, then implement in a small way—such as with pilot production—and be fully implemented at the end of the year, with virtually no remaining problems».
Alex Warren,
former Senior Vice President, Toyota Motor Manufacturing, Kentucky
Because business decisions affect many people, lean thinking organizations use this principle of agreement–building to communicate widely before any implementation. This agreement reduces resistance to lean programs and allows management to focus on the necessary actions required to succeed.
The nemawashi consensus-building approach is the fastest way to gain acceptance of lean initiatives through prior consultations before making final decisions.
14. Become a learning organization
«We view errors as opportunities for learning. Rather than blaming individuals, the organization takes corrective actions and distributes knowledge about each experience broadly. Learning is a continuous company-wide process as superiors motivate and train subordinates; as predecessors do the same for successors; and as team members at all levels share knowledge with one another».
The Toyota Way document 2001,
Toyota Motor Corporation
This principle of lean management emphasizes the need for continuous evolution through constant reflection and re-adjustment based on the learning gained in the lean journey. Businesses must not stagnate in the past, but should continuously evolve to meet current and future challenges.
Reference:
https://leanfactories.com/14-lean-management-principles/
The Toyota Way (Book) by Jeffrey K .Liker
Image Source:
https://kanbanize.com/lean-management/hoshin-kanri/what-is-hoshin-kanri
https://www.latestquality.com/andon-in-manufacturing/
https://safetyculture.com/topics/one-piece-flow/
https://www.creativesafetysupply.com/articles/kanban/
Article by: Mohamed Khaleelullah K